
"Raku" is the ancient Japanese method of firing pottery.
After each clay piece is made, it will dry for few days and then it will be bisque fired .This firing will take about
6 hours. Then the piece is glazed with certain glazes that contain metal salts and oxides and they are formulated to create a metallic look when the piece is completed. Now the piece is ready for he second firing, which is the Raku firing.
The Raku firing takes place inside a gas kiln and will take less than an hour. When the temperature reaches 1750 - 1850 degrees Fahrenheit and the piece is red hot, it will immediately be removed from the kiln with either special gloves or long tongs . The piece is placed inside a metal container full of combustible materials, like papers ,sawdust, leaves or grass. All the combustible materials will ignite right away, the flames and the smoke hit the piece in different directions and react with the Raku glaze to create very unique colors. The container is sealed very tight immediately and this exposes the piece to a reduced oxygen atmosphere. After 15-20 minutes the piece is removed from the container. Any portion of the piece that has not been glazed will turn black because of the oxygen reduction.
Raku firing is very unpredictable. No two pieces will come out the same, even if the same glaze is used on both.
The Raku fired pieces are mostly decorative pieces. They are not recommended to be used for food because the clay remains porous.
Each Raku fired piece is a-one-of-a-kind work of Art. Because of the special glazes and the process of firing , it cannot be duplicated, so it is a unique piece.
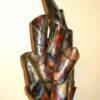